Pharmaceutical Production Line Data Collection
With biopharmaceutical enterprises accelerating intelligent manufacturing and digital transformation, SCADA (Supervisory Control and Data Acquisition) systems serve as a key automation platform for cleanrooms—enabling real-time data collection, linked control, and remote visual management of various equipment. To meet both China's GMP (Good Manufacturing Practice) and international certifications such as FDA and EU GMP, higher standards are required for network stability, low latency, security, and clean deployment.
With biopharmaceutical enterprises accelerating intelligent manufacturing and digital transformation, SCADA (Supervisory Control and Data Acquisition) systems serve as a key automation platform for cleanrooms—enabling real-time data collection, linked control, and remote visual management of various equipment. To meet both China's GMP (Good Manufacturing Practice) and international certifications such as FDA and EU GMP, higher standards are required for network stability, low latency, security, and clean deployment.
- Environmental Limitations: The workshop uses metal-reinforced ceilings, causing significant signal attenuation for traditional AP deployment (average signal strength: –75 dBm). As a result, the SCADA system cannot reliably acquire data from AGVs, PLCs, and sensors.
- Cleanliness Requirements: The cleanroom must meet ISO 14644-1 Class 8 standards. Exposed AP installations or conventional ceiling cutouts pose contamination risks.
- Business Continuity Pressure: The SCADA system supports 4K industrial cameras and vibration sensors. Existing network latency fluctuates beyond 50ms—failing to meet the strict requirement of ≶20ms.
II. Solution Overview: SCADA–Wireless Network Integrated Architecture
The proposed architecture is built on a three-layer model: Endpoint – Edge – Cloud, focusing on optimized AP deployment and network integration, with “High-Reliability Wireless + SCADA Edge Computing” at its core.
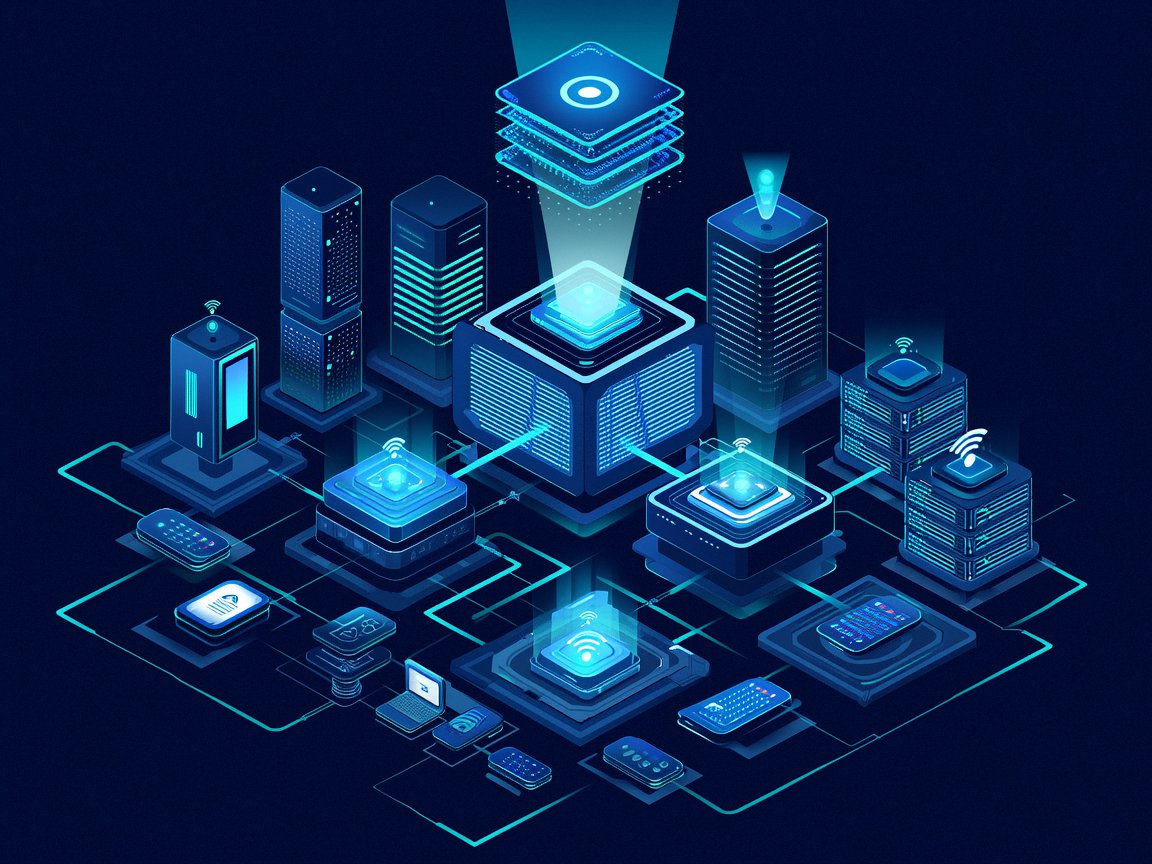
Network Layer: Customized AP Deployment
Suspended Mounting + Acrylic Protective Enclosure Design
- Optimized Placement: Using Ekahau wireless site survey tools, signal blind spots were identified. APs (AirEngine5760-51) were moved from the ceiling cavity to open areas and mounted at 2.5–3.5 meters height, avoiding metal shielding and enhancing coverage.
- Protective Cover: 5mm acrylic casing with wave penetration loss of only 0.3–0.5dB. Secured using screws and sealed with Dow Corning adhesive for IP54 rating. Top vents align with HVAC airflow to maintain AP temperature below 45°C.
- Special Scenario Adaptation: For areas like warm zones or cold storage, APs are relocated to workshop entrances with directional antennas, fulfilling SCADA's temperature/humidity sensor data collection needs.
Network Architecture Upgrade
- Dual-Band Intelligent Scheduling: Wi-Fi 6 (802.11ax) supports simultaneous 2.4GHz/5GHz operation, assigning separate channels to low-bandwidth devices (e.g., PLCs) and high-bandwidth endpoints (e.g., 4K cameras), significantly reducing latency.
- Seamless Roaming: Wireless controllers enable smart AP mesh networking, reducing packet loss to <0.1% for AGV mobility scenarios, ensuring continuous SCADA command transmission.
Edge Layer: Local SCADA Data Processing
- Deploy edge gateways to perform real-time preprocessing on high-frequency data (e.g., vibration sensors, equipment status). Only critical alert data is uploaded to the cloud, reducing network load.
- Support OPC UA protocol for IT/OT conversion, ensuring compatibility with Modbus, Profinet, and other industrial protocols. This enables smooth data flow between SCADA and MES systems.
Key Features: Integrated Network–SCADA Business Coordination
Full Wireless Coverage
- Signal strength improved from –75 dBm to –62 dBm through suspended APs.
- SCADA data acquisition success rate significantly increased.
- Acrylic enclosures achieve “zero-contamination” construction in cleanrooms, reducing cutout areas vs. traditional methods.
High Reliability & Low Latency
- Wi-Fi 6 MU-MIMO supports simultaneous multi-device access.
- SCADA command jitter <5ms, satisfying AGV emergency stop response.
- End-to-end AES-256 encryption + MAC address whitelisting blocks unauthorized access.
- Certified under IEC 62443-4-1 for industrial cybersecurity.
Customer Pain Points & Challenges
- Network–Business Disconnection: SCADA systems lacked complete wireless coverage, forcing manual entry of some PLC data—delaying production reports.
- High Maintenance Costs: Frequent SCADA alarms caused by monthly network outages led to excessive downtime and long mean time to recovery (MTTR), affecting production operations.
Customer Benefits: From Network Upgrade to Intelligent Production
- Improved Production Efficiency: Enhanced AGV dispatch performance. Real-time SCADA data drives higher productivity. Edge computing reduces cloud traffic, saving bandwidth costs annually
- Security & Compliance: Achieved Level 3 of China's MLPS 2.0 (Cybersecurity Classified Protection). Industrial firewalls block network attacks, meeting internal and regulatory audit requirements